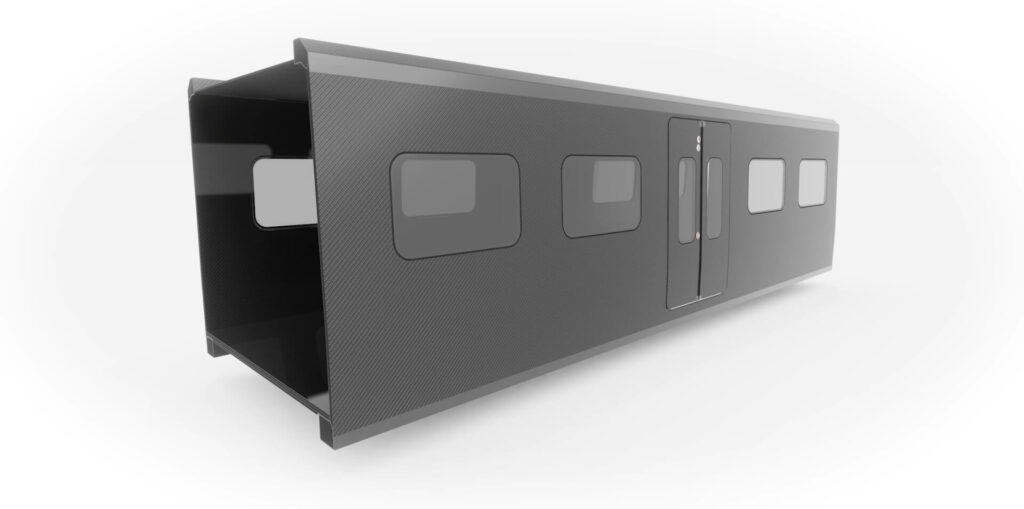
CARBODIN: Fiber composite lightweight construction for car bodies
In the CARBODIN project funded by the European Shift2Rail program, we have joined forces with European partners to develop a generic modular lightweight fiber composite design for rail vehicle bodies that allows significantly more cost-efficient production.
When designing the support structure, the restrictions of the selected cost-efficient manufacturing processes VARI = Vacuum Assisted Resin Infusion and pultrusion had to be specifically taken into account with regard to feasible geometries and fiber orientations. Thus, one focus was on the development of modular tooling systems for the VARI process, which allow the production of different fiber composite components with predominantly similar shapes by inserting different cores on only one basic tool. This allows the required number of different tools to be significantly reduced.
In addition, the use of more cost-effective precursors – resin and fibers – was taken into account in the development. Up to now, cost-intensive pre-impregnated semi-finished products – so-called “prepregs” – have mostly been used. In contrast to these, the lower-cost precursors also do not require frozen storage to prevent the premature curing reaction. The focused cold-curing resin systems also do not require an energy- and equipment-intensive curing process, but can cure at room temperature.
Cost analyses based on manufactured individual components show a savings potential of up to 25 percent compared with conventional fiber composite manufacturing processes. The lightweight solutions developed thus offer opportunities for the cost- and resource-efficient use of fiber composites for rail vehicles of the future.

